Manhole refurbishment using the Vertiliner method
Vertiliner was originally a German technology used for trenchless manhole rehabilitation. It is now used primarily for restoring circular shafts with a cone and rectangular shafts with a variable cross-section. For severely damaged manholes with cracks, gaps, deformation, missing wall segments and/or a risk of collapsing, Vertiliner is a much more economical alternative to standard methods of manhole rehabilitation using excavation.
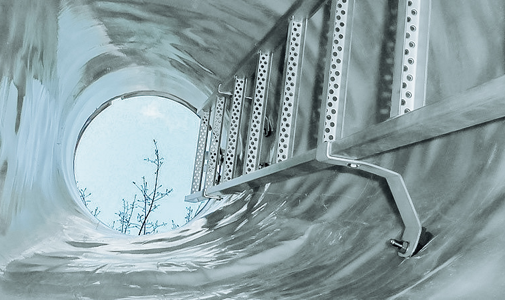
MANHOLES SUITABLE FOR THIS METHOD
Using Vertiliner, we rehabilitate circular manholes with a cone and rectangular shafts with a variable cross-section.
PROPERTIES OF THE VERTILINER SLEEVES
The Vertiliner sleeves consist of several layers of glass fibre impregnated with a special resin and cured with light. The exterior side of the liner is covered with a water-repelling and UV-blocking sealing foil. A translucent foil is situated inside the sleeve, and is removed following its installation.
HOW IT WORKS
The Vertiliner process is based on the same principle as common pipe lining. A made-to-fit sleeve of glass fibre, impregnated with a special resin, is inserted into the manhole. The sleeve is pressurised and UV lamps are used to cure the resin contained in the liner walls into a firm fibreglass. The walls of a derelict manhole receive a new self-supporting casing.
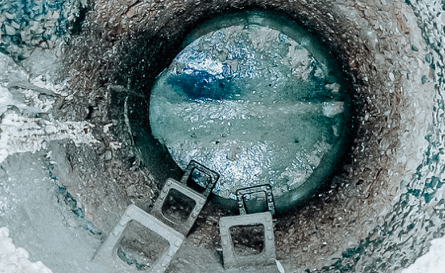
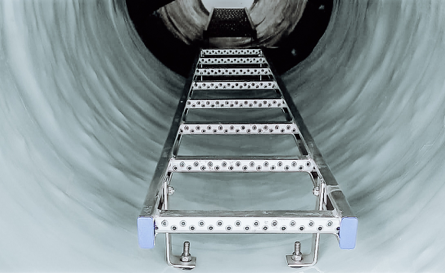
INSTALLATION PROCESS
- Inspecting and cleaning the manhole, removing footsteps or ladders
- Induction of the resin-saturated sleeve into the manhole
- Pressurising the liner with air and curing the resin using UV lamps
- De-pressurising and trimming excess liner at the top of the manhole
- Removing internal foil
- Cutting off the cured liner edge and connecting it to the former structure using an elastic sealant
- Cleaning any pipes in the shaft wall
- Rehabilitation of the bottom and berm: manual lamination, bricklayer work, or using prefabricated manhole bottom segments
BENEFITS OF THE VERTILINER REHABILITATION METHOD
- The manhole need not be directly accessible by car.
- Provides a manhole with full structural integrity.
- The cured liner is resistant to abrasion and chemicals.
- No need to secure the manhole from flooding in the main channel. Only the inlets in the manhole wall must be sealed.
- The rehabilitation is quick: the refurbishment of a 3.5-metre deep DN 1000 concrete manhole takes approximately three hours, including the refit of a ladder or footsteps.
- The manhole’s service life is extended by as much as 100 years.
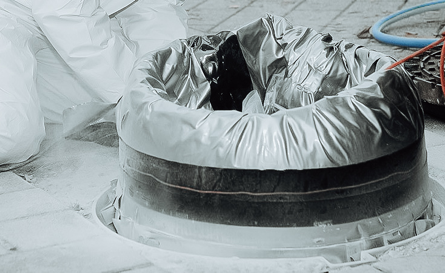
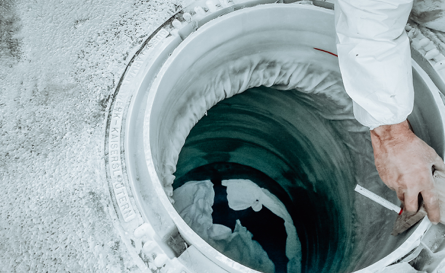
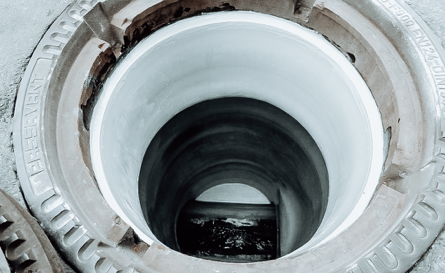
MORE DETAILS ABOUT THE TECHNOLOGY
- We always take into consideration the type and shape of the manhole cone and the lengths of all the structural elements when manufacturing the sleeve.
- The standard maximum sleeve length is 11 metres and its maximum circular diameter is 1.7 metres. We are also capable of custom making longer sleeves for deeper shafts.
- Wall thickness is adapted to the requirements on site. It ranges from 7 to approximately 20 mm.
- During the pressurising and curing process, we monitor and record essential parameters. Once the sleeve is cured, we provide the data as an official record.
- The integral seamless liner extends from the lower berm edge to the lid frame. The circular gap resulting from the curing is sealed using an EPDM rubber profile. The seal is installed approximately 10 cm from the bottom edge of the insulation.
OUR CERTIFICATION
We hold EN ISO 9001:2008 and EN ISO 14001:2004 quality certification.